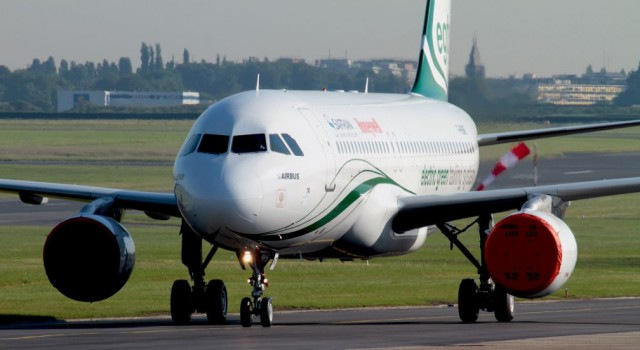
No, this A320 isn’t parked. It’s taxiing without the engines running. Check out the video after the break.
Photo: Benoît Vallet/Safran
Written for AirlineReporter.com
Airlines are doing everything they can to reduce their fuel costs. You may have taken an airline flight recently where the crew taxied to or from the runway on one engine. Or you’ve noticed that the Auxiliary Power Unit (APU) isn’t running when a plane is at the gate. Sometimes, if possible, instead of running the APU the plane can be plugged into “ground power,” getting it’s juice through a big extension cord from the terminal.
Airlines are also playing with new approach procedures that smooth out the descent and path to the runway, allowing crews to bring the power back to near-idle thrust and pretty well glide most of the way to the threshold and saving on fuel. The goal is to try and do anything to save fuel while keeping passengers safe.
Honeywell and Paris-based Safran Groupe have come up with some nifty new technology that could save airlines hundreds of thousands of dollars a year in fuel costs for each aircraft. It’s called the “Electric Green Taxi System” or EGTS, and it was recently demo’d at the Paris Air Show.
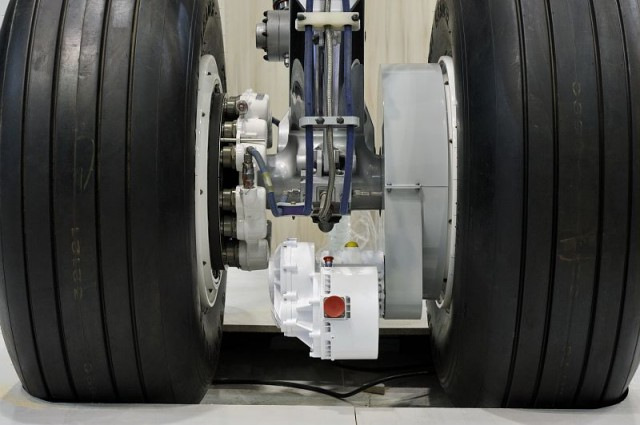
The EGTS 50 kw motor and drive system on the A320 main gear. It’s the white and grey unit.
Photo: Eric Drouin/Safran
It’s a stunningly simple idea, challenging in execution and made possible by advances in electric motor technology. Electric motors are getting smaller, lighter, and more powerful – you might have one in your hybrid car. EGTS has a 50 kw electric motor and drive system built into the outer wheel on each main landing gear. The system is powered by the APU and controlled by the pilots with a joystick console, at least in the demo A320.
The benefits of EGTS are impressive. According to Honeywell, the average short- to medium-haul narrow-body spends up to 2 1/2 hours per day on the taxiway. They figure that the direct fuel savings could be up to 4% per flight. Noise, emissions and even brake wear would be reduced, too. Engines put out a significant amount of thrust at idle, and the pilots have to use the brakes a lot to keep the speed down and stay in control.
Foreign Object Damage (FOD), which is what happens when anything but air goes through an engine, wouldn’t be an issue on the ramp or taxiways. Ramp operations would become more efficient – aircraft tugs wouldn’t be needed, the time to taxi from the gate would be reduced, and the ramp area would be safer for ground crew.
I used to be a Ramp Rat at YYZ, and I was always aware of which planes had engines running. Your day won’t end well if you get blown over by the exhaust, or worse, sucked into a mighty GE90 on a 777. With EGTS, pilots would start their engines when they reach the runway, not on the ramp.
EGTS will have a top speed of about 20 knots (23 mph) and will be able to handle sloped taxiways and ramp areas. Needless to say, Honeywell and Safran will have to do extensive testing with different taxiway and ramp conditions. It has to work in snow, rain, and on ice. I don’t think they’ll be “chaining up” on the ramp at ORD!
UK’s easyJet will be the first airline to test out the EGTS, with operational trials expected sometime this year. EGTS is scheduled to be available for A320 and 737 new-build and retrofits starting in 2016.
What do you think? Are you having an “Airplane“ moment, and seeing Captain Oveur put the plane into gear and look over his shoulder as he backs out from the gate? Is this one of those new technologies that will become standard equipment?